Cost-Effective Pipeline Insulation Support Solutions: Balancing Performance and Budget
Author:Mingde Time:2025-06-16 15:05:56 Click:194
In energy transportation and building pipeline systems, pipeline insulation supports serve as critical components for controlling heat loss and ensuring stable system operation. Achieving a balance between performance and cost has always been a focal point of industry attention. Excessive budget input does not necessarily guarantee optimal performance, while simply cutting costs may lead to energy waste and shortened equipment lifespan. How can we maximize performance within a controllable budget? This article will explore cost-effective pipeline insulation support solutions from multiple dimensions, including materials, design, installation, and maintenance.
I. Key Factors Affecting Cost and Performance of Pipeline Insulation Supports
(A) Correlation Between Material Cost and Performance
Traditional thermal insulation materials such as glass wool and mineral wool are relatively inexpensive but have limited thermal insulation and durability. New materials like nano-aerogel and composite ceramics, while possessing excellent thermal insulation and high-temperature resistance, come with significantly higher costs. Additionally, the durability of materials directly impacts long-term costs—materials with strong corrosion resistance and aging resistance, despite higher initial investments, can reduce additional expenses from frequent replacements.
(B) Cost-Effectiveness of Design Structures
Complex insulation support structures often require custom production, leading to increased design, processing, and installation costs. In contrast, standardized and modular designs can reduce unit prices through mass production and simplify installation processes. Reasonable structural optimization can enhance support performance in terms of load-bearing and thermal insulation while avoiding cost waste from redundant designs.
(C) Installation and Maintenance Costs
The difficulty of support installation directly affects labor costs. Supports requiring high-altitude operations or complex fixation significantly increase construction costs. Moreover, maintenance frequency and expenses are closely related to support materials and structures. Materials with poor weather resistance require frequent inspections, while intelligent monitoring functions, despite higher initial investments, can reduce long-term maintenance costs by enabling early fault warnings.
II. Cost-Effective Material Selection Strategies
(A) High-Value Basic Materials
Rock wool and polyurethane are common high-value materials. Rock wool offers good thermal insulation and fire resistance at a moderate price, suitable for building heating and general industrial pipelines. Polyurethane is renowned for its high thermal insulation efficiency and low thermal conductivity, widely used in refrigeration pipelines and residential buildings. Matching materials based on pipeline temperature, environmental humidity, and other scenario requirements is key to achieving a balance between cost and performance.
(B) Cost-Optimized Application of New Materials
Some new thermal insulation materials have reduced costs through technological improvements. For example, composite insulation boards combine traditional materials with nano-coatings, balancing performance and economy. Additionally, hybrid material use is an optimization strategy—applying high-performance materials in critical areas and pairing them with basic materials elsewhere can ensure core functionality while controlling costs.
(C) Material Procurement and Inventory Management
Bulk procurement can significantly reduce material unit prices. Enterprises can lock in prices by signing long-term agreements with suppliers. Meanwhile, rational inventory planning to avoid overstocking and waste, along with real-time consumption monitoring through dynamic inventory management systems, can further compress warehousing costs.
III. Economic Optimization Solutions for Structural Design
(A) Standardized and Modular Design
Standardized design reduces custom development costs through unified specifications, enabling scalable support production. Modular design allows for rapid assembly of different functional components, lowering installation complexity and labor time. It also enables precise replacement of damaged modules during maintenance, reducing overall replacement costs.
(B) Simplified Structures for Enhanced Efficiency
Removing unnecessary decorative structures or redundant supports and focusing on core functional requirements can reduce material and processing costs while shortening installation cycles. Optimizing structural layouts through mechanical simulations ensures that simplified designs do not compromise key support performances such as load-bearing and thermal insulation.
(C) Advantages of Universal Support Applications
Universal supports, compatible with pipelines of different diameters and temperatures, reduce enterprise investments in multiple specification products. Their multi-scenario adaptability not only lowers procurement costs but also improves inventory turnover rates, particularly suitable for small to medium-sized projects or applications with varying demands.
IV. Measures to Reduce Installation and Maintenance Costs
(A) Convenient Installation Solutions
Choosing pre-assembled supports or adopting installation technologies like snap-fit or quick-connect can significantly shorten construction time. Optimizing installation processes, such as pre-planning construction sequences and using standardized tools, further reduces labor costs and potential error risks.
(B) Long-Term Maintenance Strategies
Regularly cleaning support surfaces and checking the tightness of fixed components can effectively extend support lifespan. Applying anti-corrosion coatings or strengthening designs for vulnerable parts reduces maintenance frequency. Preventive maintenance plans can identify potential issues early, avoiding costly emergency repairs from sudden failures.
(C) Intelligent Monitoring to Reduce O&M Costs
Deploying low-cost temperature and vibration sensors to monitor support operation status in real-time, combined with data analysis for fault warnings, can reduce on-site inspection frequencies through remote monitoring. Utilizing automated systems to generate maintenance reports lowers labor and time costs.
V. Cost-Effective Solutions for Different Scenarios
(A) Industrial Pipeline Scenarios
High-temperature industrial pipelines can use supports combining high-temperature ceramic fibers with basic thermal insulation materials, reinforcing thermal insulation at critical high-temperature contact points while using economical materials elsewhere. Optimizing support load-bearing structures reduces replacement needs due to high-temperature deformations.
(B) Building Pipeline Scenarios
Polyurethane or rock wool supports are suitable for residential building heating and water supply and drainage pipelines, paired with standardized designs to reduce costs. Ensuring supports comply with building fire and environmental regulations avoids additional rectification costs from compliance issues.
(C) Special Environmental Scenarios
In cold regions, choosing freeze-resistant thermal insulation materials and increasing insulation layer thickness prevents pipeline freezing and cracking. In humid environments, applying anti-corrosion coatings and drainage designs avoids support rusting. For extreme conditions (such as chemical corrosion environments), replacing parts with high-performance materials balances cost and safety.
VI. Conclusion
Achieving a balance between performance and budget for pipeline insulation supports requires meticulous management throughout the entire process, from material selection, structural design, to installation and maintenance. By reasonably combining high-value materials, optimizing standardized designs, and introducing intelligent operation and maintenance technologies, enterprises can reduce both initial investments and long-term operating costs while ensuring efficient and stable operation of pipeline systems. Against the backdrop of rising energy costs and stricter environmental requirements, cost-effective insulation support solutions will become a crucial tool for enhancing competitiveness across various industries.
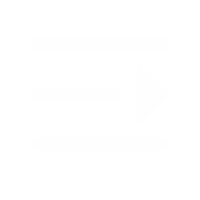
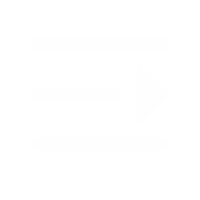
Contact:
Mobile:+86 +86 19133378808
Website:mingdepipe.com
Address: